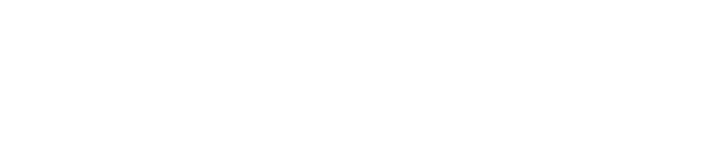

CNC Drilling Carbide Tools 3XD 3.00-20.00mm Straight Shank Twist Solid Tungsten Carbide Drill Bit

When it comes to tackling the toughest drilling jobs, the choice of tool can make all the difference. Enter the SDS drill—a powerhouse designed for precision and endurance in heavy-duty tasks. Standing for 'Slotted Drive System', SDS drills are engineered to handle the rigors of materials like steel, brick, and concrete, thanks to their unique chuck system and efficient hammer action. Whether you're a seasoned professional or gearing up for a demanding project, understanding the nuances of SDS drill technology, from the various types available to the key features and best practices, is crucial for making an informed decision. This article delves into the world of SDS drills, offering insights into their functions, applications, and maintenance to help you choose the right tool for your needs.
SDS drills, which stand for 'Slotted Drive System', are robust tools designed for heavy-duty drilling tasks. They are equipped with a unique chuck system that accommodates SDS drill bits, characterized by their slotted shanks. This design ensures a secure fit and enables the hammer action of the drill to be transferred efficiently to the bit. The hammering mechanism is propelled by a piston, which not only drives the bit forward with force but also retracts it, allowing for a concentrated hammering motion. This system is engineered to deliver high strength and reduce friction, which is essential for drilling through tough materials like steel, brick, and concrete. The slotted shank of the bit, coupled with sprung ball bearings, provides a dual function of safety and enhanced hammer action, making SDS drills a technology that combines power with precision.
SDS drills, known for their robust hammer action, are indispensable for drilling into hard materials such as brick, stone, and concrete. They come in various configurations, each designed for specific intensity and scale of work. The standard SDS drill, the original model, uses SDS accessories and is suitable for general masonry work. Progressing to SDS Plus, users find a system that is backward compatible with the original SDS but with minor design improvements, making it the most prevalent type in today's market.
For tasks demanding greater power, the SDS Max drill is the go-to option, accommodating a larger range of accessories for heavy-duty work. Although less common, the SDS Top system exists for even more intensive tasks. It's crucial for buyers to match the drill type with the corresponding accessories, as an SDS Plus drill is compatible only with SDS Plus accessories, and similarly, an SDS Max drill works exclusively with SDS Max accessories. Some SDS Max drills may allow the use of an adaptor for SDS Plus accessories, but this is not universally applicable.
The versatility of SDS drills is evident in their mode settings, offering rotation only, rotation with hammer, and hammer only options. Advanced models may feature a fourth mode for locking chisels in position, enhancing their utility for tasks like tile removal. While primarily designed for masonry, some SDS drills offer interchangeable chuck systems, allowing the use of standard drill chucks for a broader range of applications. Safety features like a clutch system are often integrated to prevent injury from sudden jams during operation.
When selecting an SDS drill, it's crucial to consider the type of drill—cordless or corded. Cordless SDS drills offer mobility and convenience, allowing use in various locations without the need for a power outlet. However, they rely on battery power, which can necessitate pauses for recharging. Corded SDS drills, conversely, provide continuous power from an electrical outlet and typically deliver more power and torque, which can be beneficial for demanding tasks.
The design of the chuck in SDS drills is specifically tailored for SDS bits, which have slots to accommodate the drill's hammer action. This hammer action is propelled by a piston, enhancing the drill's strength and reducing friction through the use of ball bearings in the bit. The choice of drill bit material is also significant, with options like carbide-tipped or chrome-nickel molybdenum steel offering durability and longevity for different drilling requirements.
Safety features are another key aspect to consider. Ensuring that the drill and bit are in good condition before use is essential, as is selecting the correct bit for the material and task at hand. Personal protective equipment (PPE) such as safety glasses, footwear, and protective clothing are indispensable for safe operation. Lastly, consider the brand as it can be indicative of the drill's quality and reliability, with various leading brands offering specialized SDS drill bits.
SDS drills, known for their robust construction, are indispensable in heavy-duty drilling tasks across various industries. Their design allows them to tackle hard materials like steel, brick, masonry, and concrete with ease. The combination of hammer action and rotary motion enables these tools to perform efficiently where standard drills might falter.
The unique slotted drive system of SDS drills accommodates specialized drill bits, which are essential for the hammer action to be effective. This action is propelled by a piston mechanism, enhancing the drill's strength and reducing friction, which is crucial when working with tough materials.
In terms of safety and precision, SDS drills stand out. They are equipped with sprung ball bearings in the bit slots, ensuring the bit remains securely in place during the intense back and forth hammering motion. This feature not only contributes to the safety of the operation but also to the accuracy and longevity of the drill bits.
The versatility of SDS drills is evident in their applications, from construction sites where they bore into concrete foundations, to renovation projects that require precise masonry work. Their functionality is further diversified with the availability of both corded and cordless models, providing options for different work environments and tasks.
SDS drill bits are engineered to endure the rigors of masonry work, where they face intense pressures and friction. To maintain their integrity and performance, these bits often incorporate tungsten carbide tips. Tungsten carbide is valued for its stiffness, which is about twice that of steel, and its ability to dissipate heat effectively. This material choice ensures that the cutting edge remains sharper for longer, promoting a smoother finish and more efficient material removal. The design of the tip is also crucial, with variations in whether the tip is welded or inserted into the drill bit affecting performance and longevity. Welded tips tend to offer faster material removal due to their proximity to the flutes, while inserted tips may retain sharpness longer but are typically suited for softer materials. The flute design is another aspect to consider, as it impacts the bit's ability to remove debris and prevent clogging. A balance in the number of flutes is essential for optimal performance in concrete and masonry drilling. Dustless or hollow drill bits represent a significant advancement, designed to extract dust through integrated pathways, minimizing exposure to harmful silica dust and enhancing the drilling process.
SDS drills, recognized for their robust construction, are designed to tackle heavy-duty drilling tasks with ease. These tools are distinguished by their slotted drive system which allows for the use of specialized SDS drill bits, enhancing the efficiency and safety of drilling operations. The hammer action of SDS drills, powered by a piston mechanism, propels the bit forward and retracts it with precision, enabling them to penetrate tough materials like steel, brick, and concrete.
For business buyers, the advantages of SDS drills are clear. They offer a combination of power and precision that standard drills cannot match, making them suitable for a variety of industrial applications. The design of the SDS drill bits, featuring sprung ball bearings, ensures a secure fit in the chuck, reducing the risk of bit slippage and enhancing user safety. Furthermore, the reduced friction levels due to the smooth action of the ball bearings contribute to the longevity of the drill, ensuring a sound investment for businesses looking for tools that can withstand the rigors of frequent use.
The versatility of SDS drills is another benefit, with both corded and cordless models available to suit different working environments. Cordless models offer the convenience of portability, while corded drills provide continuous power without the need for recharging, ensuring uninterrupted work flow. This flexibility allows businesses to select the type of drill that best fits their operational needs and work settings.
Maintaining your SDS drill is crucial for ensuring its longevity and optimal performance. Regular checks and upkeep can prevent malfunctions and extend the tool's life. Before each use, inspect the drill and drill bits for any signs of wear or damage. If any components appear compromised, it's best to replace them rather than risk a malfunction.
Proper fitting of the drill bit is essential. Verify that the bit is securely seated in the chuck before beginning your work. This not only ensures efficiency but also maintains safety standards. Additionally, the environment in which you use the drill can impact its maintenance needs. Dusty or dirty conditions, common in construction sites, necessitate more frequent cleaning to prevent buildup that can impair the drill's function.
The slotted drive system of SDS drills, with its sprung ball bearings, requires lubrication to maintain smooth operation. Check the manufacturer's guidelines for the appropriate lubricant and apply it as directed. This reduces friction and wear on the moving parts, preserving the seamless hammer action that SDS drills are known for.
Lastly, storing the drill in a dry, clean environment when not in use will protect it from moisture and extreme temperatures, which can cause corrosion and other damage. By following these best practices, you ensure that your SDS drill remains a reliable tool for any heavy-duty drilling task.
When selecting the right SDS drill bit on Alibaba.com, it's essential to consider the specific applications and materials you'll be working with. For instance, SDS Plus and SDS Max shank types cater to different levels of drilling power and are suitable for various materials, from concrete to stone. The DIN338 Straight Shank Cobalt Titanium HSS Twist Bits are designed for metal and stainless steel, indicating a focus on durability and heat resistance. Similarly, the 6mm Reduced Shank Tapered M35 Hss M42 Cobalt Twist Drill Bits are tailored for metalwork, providing a balance between flexibility and strength.
The construction of the drill bit is also a critical factor. Carbide-tipped bits, such as the YG8C Carbide Tipped SDS Max Hammer Drill Bit, offer enhanced durability when drilling into hard materials like concrete and stone. For specialized tasks, such as cutting through granite or marble, diamond rotary SDS Max Drill Bits may be the preferred choice due to their superior cutting abilities. Additionally, features like the Classic Slop Tip with 4 Cutters and U Flute design can enhance the removal of debris, increasing efficiency for concrete drilling.
Lastly, the design of the drill bit, such as the 6 Cutting Edges Hammer Drill Bit, can provide a more precise and clean drilling experience, which is crucial for masonry and brickwork. When choosing the right SDS drill bit on Alibaba.com, balance the need for precision with the material's hardness and the drill's power requirement. This careful selection will ensure that you maximize efficiency and longevity in your drilling tasks.
In the realm of heavy-duty drilling, the SDS drill stands out as a vital tool for professionals across industries. Its unique design, featuring a slotted drive system and a piston-powered hammer action, allows for efficient and safe drilling through the toughest materials. The choice between corded and cordless models, along with the selection of the right drill bit material and safety features, tailors to the specific needs of any task at hand. For business buyers, the durability and versatility of SDS drills translate into a wise investment, promising both performance and safety. Regular maintenance and proper usage are key to maximizing the tool's lifespan and ensuring ongoing reliability. When selecting an SDS drill on platforms like Alibaba.com, it's essential to consider the specific job requirements and match them with the appropriate drill and bit type. By adhering to these considerations and best practices, one can ensure that their investment in an SDS drill yields the highest efficiency and productivity for their business or project.