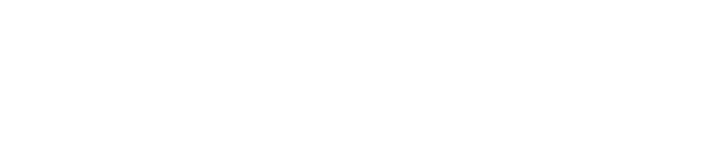

Manufacturers Wholesale S45C Steel Coupling Manufacturer OEM Flexible Omega Rubber Coupling For Sale

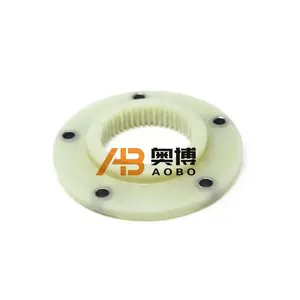
The term pump coupling rubber refers to a critical category of industrial components designed to connect pump mechanisms with motors or other types of drives. These rubber couplings are pivotal in providing flexibility and absorbing misalignments, vibrations, and shock loads in various machinery. The use of rubber in pump couplings is due to its inherent damping properties and the ability to reduce the transmission of noise and vibration between connected components.
Rubber couplings come in various configurations, each tailored to specific applications and operational demands. The flexible rubber coupling is widely used for its ability to accommodate misalignments and its ease of installation. In contrast, rubber shaft couplings are essential in scenarios where shafts are not perfectly aligned. The versatility of these components allows for their use in multiple industries, including water treatment, automotive, and manufacturing sectors.
The construction of pump coupling rubbers typically involves robust materials such as neoprene or polyurethane. These materials are selected for their durability and resistance to various environmental factors like oils, chemicals, and temperature extremes. Some pump couplings may incorporate elastomeric elements, enhancing their ability to absorb shocks and reduce wear on connected parts.
The primary advantage of using pump coupling rubber components lies in their capacity to prolong the lifespan of machinery. By mitigating mechanical shocks and compensating for alignment discrepancies, they reduce the stress on pumps and motors. Additionally, the inherent flexibility of rubber allows for thermal expansion and contraction without compromising the connection, ensuring consistent performance.
While mechanical couplings are common, the advent of magnetic shaft couplings has introduced a non-contact method of torque transmission. These systems offer reduced wear and a quieter operation compared to their mechanical counterparts. However, rubber couplings still hold a significant place in applications where a physical connection is necessary or preferred.
When selecting a pump coupling rubber, it is crucial to consider factors such as torque requirements, shaft sizes, and the degree of misalignment. The environment in which the coupling will operate also plays a role in determining the best material and type of coupling to use. It is essential to match the coupling to the specific needs of the application to ensure optimal performance and longevity.